Ardent Mills' Molinos de Puerto Rico, resilient in wake of Hurricane Maria
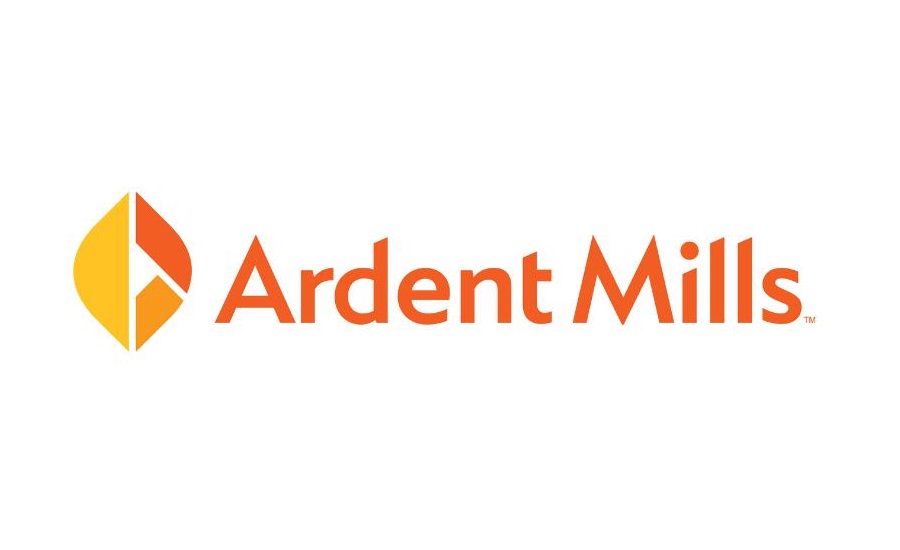
Since Hurricane Maria’s destructive forces hit Puerto Rico on September 20, 2017, Denver-based Ardent Mills’ sister company, Molinos de Puerto Rico, maintained milling operations for all but about four days. More importantly, operations at the mill in San Juan expanded almost immediately to include day-to-day assistance for employees affected by the catastrophic storm.
Jon Stuewe, president of Ardent Mills' Molinos de Puerto Rico, reports that, fortunately, the mill has no reported injuries from the storm, but many team members have faced significant losses to homes and property.
“We employ 100 people, and nearly 20 of them lost everything. One of our engineers lives in one of the only two-story, concrete houses in her area and brought 20 neighbors into her home as a nearby river flooded, engulfing the first level. One of our workers gave birth two days after the storm, when the hospitals were still running on generators, rooms were filled, and patients were marshalled into the hallways with many limited to just one bottle of water per day. Another worker was mugged and stabbed on the way home from the mill one evening,” Stuewe describes.
Despite hardships, in the storm’s aftermath, the mill community showed extraordinary humanity, hope, service, loyalty, persistence, compassion and solidarity and functioned as members of a big family working together for the same goal.
“The mill became a safe, consistent place for our team to be. We had the common goal to take care of each other, to feed the people of Puerto Rico and the hard-hit Caribbean region while serving our customers,” says Stuewe.
Emergency Preparedness
Puerto Rico is no stranger to storms, and each season, Molinos prepares by putting a hold on a leased industrial-grade generator, storing extra fuel and loading trucks in advance, which helped the mill ride out Hurricane Irma. But Hurricane Maria was different. Making landfall with winds just one mile per hour shy of a Category 5, Maria cut a diagonal swath through the island and left extreme rains in its wake, leveling much of the island and crippling services for weeks.
“We listened to our team members and got back to basics,” says Stuewe, describing how basics like water, food and clean clothes were so scarce that flying supplies in by private jets was the best solution.
To speed the response, Ardent Mills flew five team members from the company's Denver headquarters and other network sites to Puerto Rico to help staff assess damage and take the steps necessary to resume operations. Engineers, millers and health and safety specialists lived in the mill with no power, no running water and no air conditioning.
“The team who flew in even had to deal with a bat flying around the stairwell where some of them slept. But seeing this team’s effort helped lift everyone’s spirits,” Stuewe recalls.
First, Ardent Mills worked to ensure the Molinos water system was functioning – especially so their team could bring water back to their homes. They put clothes washers and dryers on site, provided three hot meals a day, and even made a barber available. Without electricity, employees couldn’t access banks, so the management provided cash and fuel.
The rest of Ardent Mills’ community of 2,400+ employees also pitched in, contributing more than $25,000 to a GoFundMe page initiated by a team member and dedicated to affected colleagues. Ardent Mills is matching $40,000.
The New Normal: Recovery Continues
As 2018 begins and the Hurricane Maria recovery continues months after the storm, Ardent Mills’ Molinos de Puerto Rico continues to supply a large portion of the grain-based food ingredients on the island and Caribbean region with its corn, wheat and rice milling.
“I had the opportunity to spend eight days on the island in two trips since the storm. After my last trip, I was glad to see real signs of improvement that are happening faster than I would have thought possible,” emphasizes Bill Stoufer, Ardent Mills COO. “The local food industry in Puerto Rico did and continues to do a great job getting food to Puerto Ricans. While food is of key importance, we learned, it is about jobs, family and providing our team with a sense of normalcy for part of the day.”
At 90 days post storm, FEMA estimates that 65.4 percent of the island has restored power, and the potable water rate is at 86 percent of pre-storm supplies. “We are off generators now, but the electric grid is not 100 percent. Gas and food are still not back to normal supplies, and most restaurants are not open,” Stuewe describes.
“There’s no way to prepare fully for an event of this scale, but we have put new systems in place, like an ultraviolet water treatment system, that will help us have clean water supplies permanently. You learn from these events,” notes Stuewe, who shares that his biggest lesson was the resiliency of his team.
“When we weren’t operating at full capacity, team members were asking, ‘What else can I do? Is there anything to clean or fix?’ They appreciated having the mill to come to, and we appreciated their ‘all-hands-on-deck’ approach to getting through this crisis together. It was a shared experience, and we grew together as a family, which we are celebrating,” says Stuewe.
Looking for a reprint of this article?
From high-res PDFs to custom plaques, order your copy today!