Automated technology can help increase efficiency in snack and bakery warehouses
Snack and bakery warehouse managers find automation adds efficiency to their operations.

Courtesy of OCME
The Bottom Line:
- Autonomous vehicles are replacing manual vehicles
- Traceability software is important
- Shipping and receiving technologies should aim to take costs out of the operation
Snack food and wholesale bakery companies are building varying levels of automation in their warehouse shipping and receiving areas, ranging from forklifts to autonomous vehicles, to traceability software and more, all in an effort to make their operations more efficient, effective, safer, and more profitable.
Forklifts and autonomous vehicles
When he walks into a snack or bakery facility, Ahmed Arif (senior director, regional office solutions, Bastian Solutions) sees a healthy distribution of manufacturing, raw ingredient, and finished product space—with, often, very little left over for shipping and receiving.

“It’s very jam-packed with equipment and different vendors,” he says. “You see a lot of forklifts driving around.… There has to be a good fleet management program, in terms of making sure they know how to service and maintain the forklifts, but I have not seen any ATVs in the food area unless it’s a massive distribution center. If you’re looking at ATVs, you’re looking at repeatable processes. If it’s highly repetitive, there’s lots of transportation time, it’s an outstanding business case.”
The Raymond Corp. focuses on automation software, connected telematic software, and operator-assist technologies layered on top of traditional trucks, says Martin Buena-Franco, product marketing manager, automation. He says his role involves bridging the needs of the field, dealership network, and sales and product management team, and ensuring that the voice of the customer is heard back at the factory.

“Those vehicles have been around for some time in distribution centers and warehouses, and they’re now making more of an inroad in manufacturing,” he says. “In the end, the customer gets consistency and the ability to redeploy workers upstream and downstream. It’s a rigorous process we follow—the optimization piece, and then a lot of times regulating telematics and labor-management systems. That gives us a lot of good visibility into what’s going on in that facility. And it’s all data-driven.”
Yale Lift Truck Technologies works with “major players” in snack and bakery, a field that handles smaller pallet weights than other industries and is focused on how many a system can load and upload, says Mark Koffarnus, director, major accounts. While forklifts can handle two to four pallets at a time, an autonomous horizontal transport can handle as many as eight, he says.
“It can be extremely common, especially in those parts of applications which is the same thing done, over and over and over again,” he relates. “They’re also packaged really well. That’s what’s interesting about snack food. It’s square boxes, easy to fit in a case dimension. Autonomous vehicles do not like packaging that’s out of the norm.”
Yale Lift concentrates heavily on the receiving side, usually at the beginning of the operation, and hones in on time-and-motion studies, Koffarnus says. “How can we get people walking fewer steps? How can I get a product off the truck faster? How can I get labeling done more quickly? If you find efficiencies in the front end, many times, you’ll be saving steps, saving time, making it more efficient, both through the warehouse until the shipping dock.”
The main reasons to turn to autonomous vehicles to replace manual ones are labor savings, product consistency, and lack of damage to the products or warehouse, says Shawn Semer, director of sales and marketing, global automation, for Signode Industrial Group. “It always surprises me when I talk to customers about their ROI, and see a dramatic number, not only in health-and-safety but also damage to the racking,” he reports.
Working with manual vehicles, Semer says, taking products from the dock can be challenging because they’ve been shaken around and are sitting on an angle. “You see all the gyrations they need to do to get the forks into the pallets. Unloading is extremely difficult. Interfacing once the products are unloaded onto the dock, into an automatic storage retrieval system, is a fantastic location for automation. It’s consistent. The vehicles are working through the [employee] breaks. The system is making sure that the products are staged there, so the operator only have to make a short travel from the staging location into the trailer.”
Moving from a forklift to an automated vehicle can reduce both damages and manual labor costs, says Fabio Forino, sales manager at OCME America. “You can work 24–7. The more you work, the faster you’re going to have the payback from the investment. … With a forklift or other non-automated vehicle, you’re exposed to the fact that you can ship whatever you got first, not the oldest in the plant. With [automated vehicles], you can always make sure you are shipping the oldest product.” Those whose jobs are automated can be redeployed elsewhere in the plant, he adds.
Traceability software
The use of traceability software starts with the customer’s warehouse management system in determining, within their facility, where they have ingredients, and where they have finished goods, Buena-Franco says. “If it is a critical pallet or ingredient that we need to track, or follow, we can use our sensors to find it in the facility, if necessary, as opposed to having to scout out and walk the facility,” he says. “We can certainly provide a lot more granularity. We can track it more closely.”
The right use-cases depend on the facility, the customer, and what they want to accomplish, Buena-Franco reports. “We can create zones within the facility,” he says. “If you have a packaging area, and a lot of people there, we can actually keep assets or trucks from going into that area. Or say you have overhead infrastructure in the building—we don’t want the operator accidentally forgetting … and damaging infrastructure.”
Raymond’s technology leverages telematics or labor management systems “so we know throughout the day what the traffic looks like, tied to the work management system,” Buena-Franco says. “We can time it in a way to reduce congestion. You have a lot more people, typically, on the first shift. If you extend [processes] out, you can reduce congestion.”
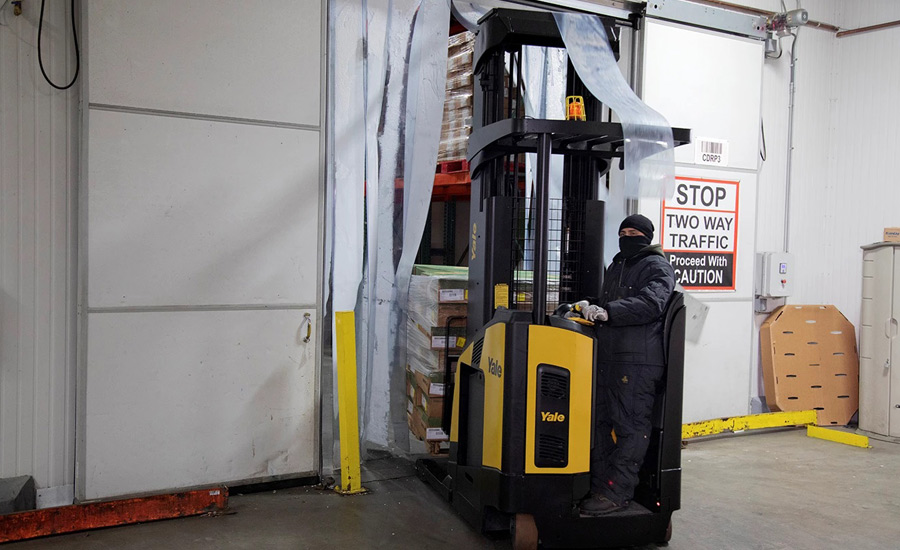
Traceability software is hugely important, Semer states, reflecting on the number of times he’s walked through warehouses with products that appear to have a year’s worth of dust on them. “Especially on the snack side, where you’re talking about fresh materials, you want to make sure you’re pulling fresh product out, the older product first. That happens when you have full traceability of where the product is inside the warehouse.”
Another reason for traceability is to make sure that when shipping out a load of product, it doesn’t need to be collected from every corner of the warehouse, Semer says. “You don’t store all of that one flavored chip in the same area,” he says, adding that to avoid traffic jams, “You don’t want all your automation to go to the same area. You scatter that product to where multiple automation assets can retrieve that product.”
Traceability software enables you to better manage traffic and talk with the production line, Forino says. “Especially for the food business, with expiration dates, and ingredients, there are many points that are very important,” adds Alessandro Morini, vice president of sales, North America, for OCME. “Traceability is a must.”
Food companies want to keep their names out of the newspapers unless the publicity is being generated by their own marketing departments, Arif says. “Reputation is everything,” he says. “That has to do with traceability, and making sure you have a robust management system that allows you to understand lot control. If your product need to be serialized, you can track it back to what lot it was produced. That’s super-critical.”
Due diligence on the software and hardware involved in tagging products is also important, Arif says. “And how well the bar-coding or application hardware is; how well it integrates with other machines in the plant, is very important,” he says.
Other innovations
Shipping and receiving is a natural area to start when performing an implementation in a manufacturing setting, Buena-Franco says. Typically, trucks are still unloaded manually, although his company is investigating autonomous loading, and it’s in the final stages of launching the ability to build a lane, or matrix, for staging. “That’s typically not within the capabilities of an autonomous system,” he says. “We can offer that in the very near term.”
Broadly speaking, shipping and receiving technologies should be geared towards taking costs out of the operation, Koffarnus declares. While technologies applied to forklifts have focused on preventing damage to the facility or product, or successfully avoiding pedestrians, that’s not necessarily the main reason snack and bakery producers deploy them.
“A lot of them look to the technology not for the safety aspect, but for the efficiency it provides,” he says. “All the sudden, a novice operator becomes almost as efficient as a seasoned operator because they have these technologies protecting them from doing wrong things. It makes their learning cycle much, much shorter. Even if you have a turnover issue, you have a more productive workforce because you don’t have a workforce making bad decisions.”
Adding automation to one aspect of your shipping and receiving operation oftentimes leads to light bulbs going on in other areas, Semer says. “You start to see that you can use that same asset, vehicles or automatic retrieval, to manage the materials to go into your production. What that does, typically, is it helps with your [purchase] justification. You can look at that asset as constantly being full, if you will. If it’s a mobile vehicle, coming from production and going to the automatic storage retrieval system, and from there to the dock, when you have materials coming in on those same docks, the same vehicle can make the return trip.”
Other technologies used in the shipping and receiving area include a portal accessible on a mobile or laptop device to be able to see everything that’s going in the warehouse, Forino says. “We can organize the warehouse, optimize the space, based on the application, and based on the customers’ needs. You can work on the floor, you can be selective. We can always monitor.… We can prepare all the materials, the finished goods are going to be shipped.”
“The system can optimize the workforce,” Morini adds. “You know every single pallet, the position, other information. You can work 24 hours.”
Arif has seen making sure trucks get in and out in a timely manner as a significant pain point, related to yard management. “Something else I’ve seen as problematic that can be solved by better management of the semi-trucks in their yard, just making sure the drivers are not waiting forever to get loaded up,” he says. “A robust yard management system is pretty critical. Otherwise, it can affect the quality of the product leaving your building.”
Looking for a reprint of this article?
From high-res PDFs to custom plaques, order your copy today!