Palletizing solutions incorporate robotics
New systems handle a variety of packaging formats.

The Bottom Line:
- Feature human-machine interface and end-of-arm-tooling
- Maximize space efficiency
- Stacks are easily arranged to meet retailer specifications
The evolution of palletizing is linked to robotics. In fact, robotic palletizing of flexible bags in snack and bakery plants is a reliable way to handle variations in weight. Modern robotic palletizers also can be equipped with programmable, HMI (human-machine interface), and end-of-arm-tooling (EOAT) that allow manufacturers to quickly switch between a variety of bag sizes, weights, and materials.
While robots have long been used to construct pallets, their role is expanding as their capabilities improve, according to the “2021 End-of-Line Equipment Report” released by PMMI, Reston, VA. “Robotic palletizers are ideal for constructing stable pallet stacks that maximize space efficiency, allowing manufacturers to easily adapt to a variety of packaging formats, from flexible to rigid,” the report states. “Stacks are easily arranged to meet retailer specifications.”
While robotics is one of the solutions available to manufacturers looking to automate their palletizing operations, it is not the only option, according to the report. “A variety of machine-based, non-robotic automation strategies exist that accomplish fully automated palletizing and eliminate the need for manual labor.” These non-robotic systems are attractive to some manufacturers because they cost less than robotic systems.
Beyond robotics, the latest palletizing equipment offers space-saving features as well as integrated stretch wrapping systems to facilitate the shipping process. See below for some of the latest offerings.

Company
A-B-C Packaging Machine Corp.
A-B-C Packaging Machine Corp., Tarpon Springs, FL, recently introduced a compact palletizer, the Model 72AN, designed to fit in production areas where space is limited. It is fully automatic and offers all the flexibility and efficiencies of A-B-C’s larger models, but occupies up to 30% less floor space than other floor-level palletizers, the company reports.
Another area of recent advancement: all A-B-C palletizers are now smart machines that offer connectivity to plant-wide control. All operating data, from the drives all the way down to the component and sensor level, can be readily accessed at the HMI as well as the factory control station, according to Bryan Sinicrope, vice president of marketing and integrator sales.
A-B-C palletizers can configure packages in each layer to have “graphics or labels out.” This can increase efficiency at the warehouse or retail outlet, as product contents and ship dates are easily obtained via a quick scan. “Also, our pallet builder enables configuration of new pallet and layer configurations at the HMI,” Sinicrope says. “We can palletize four patterns within one pallet, offering enhanced flexibility for snack and bakery producers who are shipping to retail outlets.”

Company
AFA Systems Ltd.
AFA Systems Ltd., Brampton, Ontario, recently developed a combination case packer/palletizer, the TR-CPP - Combination Case Packer Palletizer. The system automatically erects a case and places it on a shuttle. A gantry robot collates, and the load system packs the correct pack pattern in the case. Afterward, a gantry robot picks up the completed case and places it onto a pallet. The machine features two loading stations with automatic discharge conveyors.
The system provides many benefits to bakery and snack food producers, according to Eric Langen, vice president of sales and marketing. “Its mono-block design reduces the footprint compared to traditional cells and it utilizes one control system to ensure efficient handshaking between case packing and palletizing. The TR-CPP also has two pallet stations to ensure no interruption to production when a completed pallet discharges.” AFA palletizers have integrated stretch wrapping systems to facilitate the shipping process. This process is becoming more automated as automated guided vehicles deliver pallets right into dry van trailers.
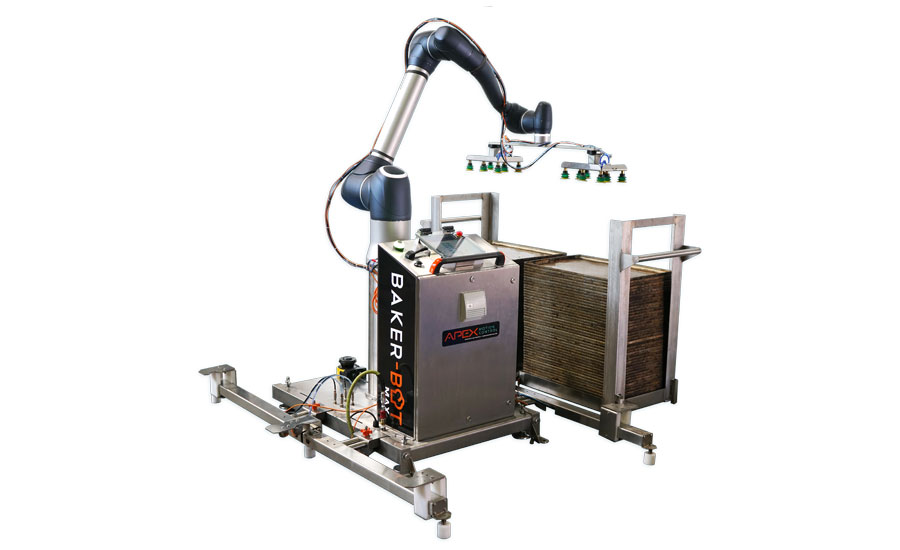
Company
Apex Motion Control
The Baker-Bot MAX is an industrial user-friendly cobot that is designed specifically to handle food and bakery palletizing tasks. The Baker-Bot MAX cobot utilizes the smallest footprint possible while helping address the labor crisis, and offering a quick deployment and ROI. With a payload of 44 lbs, a reach of almost 70″ and a palletizing height of 89″, the Baker-Bot MAX can be quickly set up just about anywhere on the plant floor with minimal guarding.

Company
Colborne Foodbotics
Colborne Foodbotics, Lake Forest, IL, offers a palletizing system that leverages the design features of its robotic packaging systems. A multi-purpose, end-of-arm tool is designed to execute multiple tasks. Within the system, the robot un-stacks pallets on a unit basis to prepare for loading; the same robot and EOAT picks cases or trays and loads them onto the pallet. The robot also can place slip sheets. “This is a great option for users who need to fit a palletizing system in a small footprint,” says Rick Hoskins, president.
“By using palletizing robots, we are able to match any payload application,” Hoskins adds. “The integrated handling systems for product presentation are custom-made for the most challenging projects. Our systems can be integrated to Allen Bradley control systems or stand-alone internal robot controls. We also integrate pallet wrapping, label and printing technologies into these systems.” Colborne Foodbotics also offers automated removal of pallets to downstream distribution areas or trucks. Through its Autonomous Mobile Robot system, pallets are removed after completion and delivered anywhere within a facility.

Company
Columbia Machine Inc.
Columbia Machine Inc., Vancouver, WA, has developed a servo-controlled star wheel turner that is well suited to end-of-line palletizing solutions for small packages. “The Columbia star wheel turner is especially well suited to the snack food industry due to its flexibility in handling a variety of package types and sizes and where there are many contract package manufacturers,” says Ted Yeigh, marketing manager, Northwest Region, and Palletizer Div.
Columbia palletizers are equipped with HMI. “When combined with standard changeover components, any Columbia palletizer is capable of zero time and zero tool changeovers with no operator intervention,” Yeigh adds. The company also has developed a fork-style load, double-stack solution for end-of-line and shipping. This allows a completed load to be lifted up above a pallet conveyor line and wait for another load to come under and stop at the double-stack station. “This is especially relevant to the snack food industry where double-stacked loads may be loaded into trailers to maximize shipping efficiency.”

Company
Delkor Systems Inc.
Delkor Systems Inc., Minneapolis, MN, has introduced a robotic palletizing system with an integrated stretch wrapper that builds the pallet on the stretch wrapper. This has two benefits, according to Dan Altman, vice president of sales and marketing. First, there is no need to move a fully built (but unstable) pallet downstream to a stretch wrapper. Second, floor space is saved with the elimination of a pallet transport conveyor. “The modular design of this system allows for products and pallets to come in and out from any side of the pallet cell. It also accommodates slip sheets, tier sheets, and top sheets with ease.”
Delkor’s robotic palletizing system allows the forklift driver or automated guided vehicle to pick up a fully wrapped pallet and bring it to the desired destination, or directly onto a truck. “In conventional setups, the fork lift driver has to move the unwrapped pallet to a standalone stretch wrapper, which takes time and reduces efficiency as unwrapped, unstable pallets can shift in transport,” Altman notes.
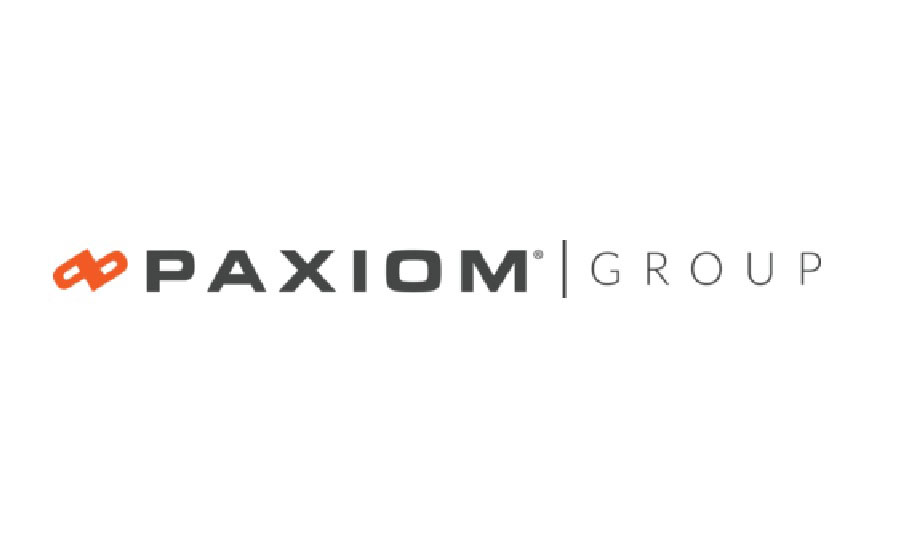
Company
Paxiom Group
Paxiom Group, Las Vegas, offers the EndFlex Z.ZAG Palletizer, which uses vacuum generators to pick up cases one at a time and place them on a pallet from above. Its suction capacity is capable of lifting 40-lb boxes at speeds up to 360 boxes per hour.
The position of each case is calculated automatically according to the desired pattern and the dimensions of the case; the Z.ZAG palletizer locates all cases on one pallet and upon completion starts filling the next pallet as the first pallet is replaced. Using this end-of-line application is less costly than using conveyors to transport cases to a high-speed palletizer, the company reports. Designed to SCARA standards in a compact footprint, the Z.ZAG is created for multi-pack patterns for column-stacked and interlocked configurations. It is servo-driven with PLC controls and a color touch screen to make set up and operation user-friendly.

Company
Yaskawa Motoman
Yaskawa Motoman, Miamisburg, OH, has introduced the HC10DTP, HC20DTP, and HC30PL collaborative robots. All three can be used for snack and bakery palletizing applications because they feature IP67 environmental ratings and come with food grade grease as standard. The HC30PL is designed for use in collaborative palletizing operations, offering a 30kg payload with a maximum reach of 1,700mm.
All three models feature an ISO 9409-1 tool flange and M8-A code I/O connection, which allow many third-party end effectors to plug-and-play. “Several integrators and technology providers have created modular solutions based on the HC-Series robots,” says Chris Caldwell, product manager. “Solutions vary in complexity but many are user-friendly and feature HMIs that allow for quick deployment.”
Beyond new robot models, Yaskawa recently updated its PalletSolver software. The PC-based software is used to configure a palletizing work cell, manage the product and pattern database, and create robot jobs. The robot controller-based runtime enables peak palletizing performance, according to Caldwell. In early 2023, the company plans to launch palletizing software for use with its tablet-style Smart Pendant.

Company
Robotiq, Lévis
Robotiq, Lévis, Québec, Canada, offers the Robotiq Palletizing Solution. A material handling copilot guides the user through the process of defining the palletizing process. Once the user enters the box weight and dimensions, he or she can drag and drop the pallet layout on-screen. “The Robotiq Palletizing Solution takes it from there,” says Ryan Weaver, commercial vice president. “The cobot automatically picks and places the boxes of product exactly where they belong on the pallet. Once the stack is high enough, the servo-controlled vertical axis coordinates the lifting of the robot, so pallets up to 108″ can be built quickly.”
“Due to the fact that cobots can operate safely around humans, along with the lightweight, compact form factor of the cobot and palletizing cell, the deployment is more compact than traditional automation installations,” Weaver continues. “This means less floor space is taken up, and it’s easier to automate multiple lines within a tight space.”Looking for a reprint of this article?
From high-res PDFs to custom plaques, order your copy today!