Package Handling with Care
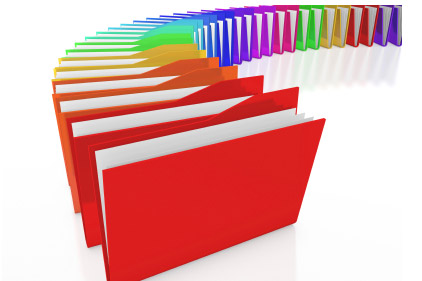
A critical aspect on any production line, the package handling function
may require one conveyor section, multiple lanes or hundreds of
integrated material handling accumulators, elevators, lowerators,
robotics, controllers and more. We asked several manufacturers what’s
new in package handling equipment and systems to make your
manufacturing operation more productive.

Lauren R. Hartman, Editor-in-Chief
Several trends in package handling systems are driving sales and impacting bakers, snack food manufacturers and other food processors. Despite the slow economy, packaging equipment has experienced a real growth curve the last 18-24 months. As companies look to increase output, add items, change processes and reduce costs, they often turn to automation. And cost is one of the most critical aspects involved with packaging handling equipment.
At Delkor Systems, Circle Pines, Minn., today’s key drivers are retail-ready/shelf-ready packaging concepts and machine versatility. “Another factor is fast, repeatable changeover due to product variety demands,” reports Mike Wilcox, vice president of sales, marketing and aftermarket sales. “Delkor has developed and launched eight new machines over the last 18 months that already account for almost 40% of new machine sales. These machines incorporate ideas that address the aforementioned trends and have allowed us to grow our business.”
Many cutting-edge developments position Delkor to provide attractive packaging, enabling the company to better serve customer needs, Wilcox adds. In addition, tool-less changeovers have been a customer desire for some time. “But also minimizing the changeover time requirement is equally important,” Wilcox points out. “The third element of this trend is fast startup. A fast changeover is quickly negated if continual adjustments are necessary for optimum performance.”
Clearly, demands call for more equipment sanitation and higher performance. “The new standards for cleanliness and sanitary design are a fact of machine design today,” he says. “Dry-product operations are using sanitary design elements formerly found in dairy and meat operations, while the latter industries require higher levels of sanitary design than before.”
Delkor’s Trayfecta carton-and-case forming machine line is at the top of its product sales today. The machines form cartons, cases and trays in either paperboard or corrugated materials. The Trayfecta M series of mechanical formers incorporates many safety and reliability features for which Delkor packaging machines are respected. Trayfecta S Series formers apply servo-drive controls to critical machine functions, thereby increasing speed and flexibility, while retaining traditional safety and reliability attributes. Its Spot-Pak machine line is also innovative for secondary packaging applications because it not only eliminates a corrugated case, but the corrugated trays as well. The machinery can load primary product containers onto flat pads.
A critical factor in designing new package handling systems today that Delkor faces includes the ability to maintain line operation while sorting and removing damaged or unsalable product to prevent downtime and bad product getting to the pallet, according to Wilcox. “Also, minimized material content and overall utilization places a significant demand on product and package handling machines. Low-height trays, simple corrugated pads, shrink-bundled products and lightweight materials require more precise machine movement and accurate repeatable setup. Our customers would also like to see precision package forming, managing damaged product out of the line, minimizing product rework and lower operating costs. Creating flexibility in machine design is also important to readily adapt to a variety of material and package options. But, delivering higher standards of operation while remaining cost effective is another key element.”
Despite poor economic reports though, Wilcox sees package machine sales to be very good for many companies at this time.
Costs are an issue
When it comes to costs, everyone is trying to control them, admits Derek Jones, senior marketing product manager at Lantech, Louisville, Ky. Jones says his firm experienced a downturn in sales back in 2008 like everyone else in the industry. Some bakers and snack producers are taking advantage of the current economy by upgrading and/or retrofitting existing equipment with the latest innovations.
“Many understand that the return on investment with recent innovations will have a short payback period,” says Jones. “But 2011 has been a banner year for sales. With that in mind, one of the best ways to keep tabs on costs is to make sure that shipping charges are correct. By weighing every load you ship for quality and freight costs, you are able to ensure that you’re being charged correctly.”
In addition, he says that understanding customer’s needs help his firm continue to be the leader in innovation in the industry. “Customers want peak performance,” Jones states. “They also want all-in-one weighing and stretch-wrapping machines that have a small footprint, are durable and keep operators safe. But it’s a challenge sometimes in educating our audience that all stretch wrappers are not [created] equal.”
Lantech’s EZ Weigh integrated scale with semi-automatic stretch wrapper, which was launched at September’s Pack Expo Las Vegas, meets those demands, he points out. “EZ Weigh weighs every load to optimize load quality and freight costs. The machine saves space and has a new, tilted skirt turntable design. The turntable resists impacts from fork trucks and pallet jacks. The weighing system is integrated under the turntable instead of with the entire machine. This helps improves weight accuracy as items only on the turntable are weighed.”
Improvements in containing loads is one of the greatest opportunities for growth in the package handling equipment market, Jones points out. “It’s critical to ensure that every load shipped meets ‘good load’ criteria. Good loads are bonded to a pallet to prevent shifting during transit. The stretch film used must be evenly applied to the load, without long or dragging film tails that could get caught on downstream equipment.”
Hygienic design counts
Dorner Manufacturing Corp., Hartland, Wis., agrees that the focus is not only equipment’s material construction but also hygienic design. “Customers are of the mindset that they will own this equipment for a long time,” says John Kuhnz, director of marketing. “Paying attention to equipment design and construction leads to a lower cost of ownership over the life of the equipment. This is a direct result of changes in overall cleaning practices in terms of increased frequency and to include areas in the facility that otherwise are not considered. In addition, the packaging lines in some applications are in closer proximity to the production areas, so customers opt for stainless steel and other corrosion-resistant materials. This is driving sales of sanitary designed and constructed equipment. It’s also impacting accessories often used with the equipment.”
Kuhnz says that customers indeed expect higher performance and some of it focuses on cleaning. “They want to minimize planned downtime and, if possible, eliminate unplanned downtime,” he points out. “Designing equipment with features that make cleaning easier and more effective reduces planned downtime for sanitation or allergen washes. Designs on our equipment like tip-up tails, belt lifters and clean-out windows address these requirements. Customers are able to access these components, to clean the inside of the conveyor frame in seconds without tools.”
He believes that sanitary equipment is evolving every day. “Each time a piece of equipment is manufactured, suppliers and customers work on ways to make the equipment more sanitary.”
Dorner continues to invest in “smart” conveyance. “Smart” features go beyond sanitation and into conveyors that are easier to implement, communicate and interface with emerging technologies and packaging, Kuhnz says. The company offers a diverse range of conveyors and unit-handling solutions to meet these trends. There are conveyors for dry areas as well as wipedown and washdown platforms, available in both aluminum and stainless steel. “Each conveyor platform has hygienic design features required for a targeted environment within the food production facility,” Kuhnz reports. “And each platform has a set of conveyor features or accessories that allows for tailoring to each customer’s application.”
Where Dorner’s washdown systems are concerned, the most popular feature is the tip-up tails, which allow for quick access to internal frames for sanitation. On its dry conveyor platforms, the SmartSlot creates a smooth side on the exterior but still allows for the fast attachment of automation components. “In other words, there are no T-slots that could catch product debris,” he says.
The AquaPruf sanitary conveyor line is also designed for fast, effective sanitation that allows production lines to start running again quickly. “This is a real dollar saver,” Kuhnz points out.
Another trend that Dorner sees is the increased use of flexible package and pouches. “They bring new challenges with respect to their handling,” Kuhns acknowledges. “Another trend is future needs planning with package handling systems. Can a system be designed for a larger package, a smaller package or accept a 50% increase in volume? These discussions are taking place on each system design as companies look for greater ROI from packaging equipment automation. But for our role in package handling systems, I’d like conveyors to lead the way in hygienic design and sanitation features,” says Kuhnz. “Sanitary equipment is evolving every day.”
Robots get a grip
Weldon Solutions, York, Pa., builds robotic palletizing systems that it considers are the most flexible way to load multiple pallets of different products at the same time. “This requires that the robot’s end-of-arm tool (EOAT) be flexible enough to securely handle a variety of items,” notes Charles Gales, manager of automation sales at Weldon. “Our UniGripper has a matrix of valves that create a vacuum across the surface, and is capable of picking up one or multiple cases,” he says. “The compliant face of the UniGripper only creates a vacuum where cases are present. That allows for handling of different case sizes with no changeover. This is particularly helpful for CPG companies that change case sizes frequently during the production day or over time. The UniGripper can also automatically adapt to new case sizes. Once a new product or product size is programmed into the robot, that new information is ready to be handled by the UniGripper.”
Lowering cost of ownership
Dynamic Conveyor Corp., Muskegon, Mich., launched a new line of conveyors to the food processing and food packaging industries at PackExpo Las Vegas 2011, says Jill Bartka, president. “In addition to being quick and easy to clean, which saves time and money, the new line offers a unique benefit of reconfiguring the conveyor layout when the needs of the processor change.”
The company’s DynaClean conveyors are eco-friendly and sustainable, she points out, and reducing the ecological footprint is becoming a priority for many food companies. “Lowering the total cost of ownership is typically even more important to processors as costs continue to rise and it becomes more and more difficult to make a profit,” she says. “The DynaClean line is a response to these needs by allowing the end user to quickly and easily clean the conveyor, saving time and labor and other resources. This also saves changing the conveyor configuration with new segments of a different length or angle, preventing the conveyors from sitting unused and forcing the processor to purchase a new conveyor.”
Bartka says that when her firm designs a new package handling systems today, one of the most critical factors is that time is money. “Customers need conveyors that are quick and easy to clean. We design systems to include optional belt lifters that allow for access within three seconds to the underside of the belt and the internal conveyor components. The ability to remove the belt, belt supports, the motor and the return within in a few minutes without tools gives easy and very quick access for a thorough cleaning and sanitation. The conveyor can be reassembled after cleaning almost as easily as taking it apart.”
While the snack food and bakery markets are relatively new to Dynamic Conveyor, Bartka says there are great opportunities. “Educating processors on these new options in conveying that weren’t available just a few months ago is exciting for us and the processors. We’re eager to educate them on the fact that they can reduce their costs of conveyor ownership with a quick and easy-to-clean system that’s reconfigurable.”
Partnering with Intralox, Harahan, La., Dynamic Conveyor will soon offer an option for Intralox’s ThermoDrive belts on DynaClean conveyors. “An innovative, patented technology, ThermoDrive is the first to combine the best features of modular plastic and traditional flat belts.”
Solving denesting difficulties
Customers are also looking for solutions to difficult denesting tasks brought on by the need to reduce shipping costs. Because tray and clamshell package manufacturers are asked to reduce the size and weight of their denesting features, trays now nest closer together, making them even more difficult to separate, states Paul Grieger, inside sales for Axis Automation, Hartland, Wis. “Tray and clamshell manufacturers need to be able to make trays with much smaller denesting features, or possibly even none at all,” Grieger says. “We’re seeing a sharp increase in demand for our AXIS denester, which doesn’t use conventional denesting methods.”
Launched in the spring, the AXIS denester was developed to answer the call of rising fuel surcharges, increasing labor costs and a demonstrated need to perform without suction cups. It denests difficult containers such as certain foam structures. Because of this, trays don’t need to have flat bottoms. “Trays can now have ridges across the entire surface below the product, which translates into less product breakage and better presentation,” he says. “Cookies or crackers can stay nested in the tray. And the denester’s design works well with trays that have much smaller denesting features or in some cases, none at all. Smaller denesting features means that trays nest closer together. That’s ultimately better for the environment. Less space between trays means fuel savings because there are fewer cases to ship for the same quantity of trays or clamshells.”
Grieger agrees that sanitation is always an issue. “A stainless-steel construction makes cleaning and sanitation much easier. And easier changeovers are also very important. High performance is always a requirement as well. A denester can be well built, easy to clean and a real bargain, but if the machine isn’t up to the task at hand, it’s going to be moved to a dark corner where it will sit and gather dust.”
Display-worthy and enviro-friendly
Display-ready packaging that significantly reduces labor costs when stocking shelves is also seeing big demand at Eagle Packaging Machinery, Miami. “Another trend we see is packaging that’s environmentally friendly-using less packaging to reduce the overall packaging footprint,” says John Brown, sales and marketing coordinator for Eagle. “Our POLOK tray former uses no glue or tape, which facilitates recycling. Customers also look for machines that can pack or form different tray sizes and are fast and easy to change over. The flexibility of the POLOK tray former allows us to accommodate various tray-size ranges unique to each customer.”
The former creates one- and two-tuck, multi-tuck and intricate trays, with or without a lid, in small and large-size formats. “Secondary packaging that doesn’t touch the product directly, productivity is paramount,” Brown adds.
In addition, the Boxxer Auto Lock case erector uses no tape or glue when erecting RSC/HSC-style cases with auto-locking bottoms. Built with a low maintenance mechanical drive, a heavy-duty welded steel frame and interlocked safety gates and doors, the Auto Lock provides quick-size changeovers in a compact footprint. Venturi vacuum technology is used to erect the trays, and all functions are controlled with a PLC color touchscreen. Also using vacuum technology is Eagle’s Z.ZAG palletizer, which automatically picks up one or two cases and places them on a pallet. The system can be used with several production lines.
“There’s another trend in the industry to lighten the container board without sacrificing the required strength and integrity needed, all of which will influence the future designs of equipment,” Brown points out. “Today, we see more need for equipment that’s simpler for operators to learn and use and for maintenance staff to service.”
Regardless of what’s being packaged and shipped, this and many other package handling systems are being designed to fill the bill on baker and snack manufacturer needs.

Lauren R. Hartman, Editor-in-Chief
Several trends in package handling systems are driving sales and impacting bakers, snack food manufacturers and other food processors. Despite the slow economy, packaging equipment has experienced a real growth curve the last 18-24 months. As companies look to increase output, add items, change processes and reduce costs, they often turn to automation. And cost is one of the most critical aspects involved with packaging handling equipment.
At Delkor Systems, Circle Pines, Minn., today’s key drivers are retail-ready/shelf-ready packaging concepts and machine versatility. “Another factor is fast, repeatable changeover due to product variety demands,” reports Mike Wilcox, vice president of sales, marketing and aftermarket sales. “Delkor has developed and launched eight new machines over the last 18 months that already account for almost 40% of new machine sales. These machines incorporate ideas that address the aforementioned trends and have allowed us to grow our business.”
Many cutting-edge developments position Delkor to provide attractive packaging, enabling the company to better serve customer needs, Wilcox adds. In addition, tool-less changeovers have been a customer desire for some time. “But also minimizing the changeover time requirement is equally important,” Wilcox points out. “The third element of this trend is fast startup. A fast changeover is quickly negated if continual adjustments are necessary for optimum performance.”
Clearly, demands call for more equipment sanitation and higher performance. “The new standards for cleanliness and sanitary design are a fact of machine design today,” he says. “Dry-product operations are using sanitary design elements formerly found in dairy and meat operations, while the latter industries require higher levels of sanitary design than before.”
Delkor’s Trayfecta carton-and-case forming machine line is at the top of its product sales today. The machines form cartons, cases and trays in either paperboard or corrugated materials. The Trayfecta M series of mechanical formers incorporates many safety and reliability features for which Delkor packaging machines are respected. Trayfecta S Series formers apply servo-drive controls to critical machine functions, thereby increasing speed and flexibility, while retaining traditional safety and reliability attributes. Its Spot-Pak machine line is also innovative for secondary packaging applications because it not only eliminates a corrugated case, but the corrugated trays as well. The machinery can load primary product containers onto flat pads.
A critical factor in designing new package handling systems today that Delkor faces includes the ability to maintain line operation while sorting and removing damaged or unsalable product to prevent downtime and bad product getting to the pallet, according to Wilcox. “Also, minimized material content and overall utilization places a significant demand on product and package handling machines. Low-height trays, simple corrugated pads, shrink-bundled products and lightweight materials require more precise machine movement and accurate repeatable setup. Our customers would also like to see precision package forming, managing damaged product out of the line, minimizing product rework and lower operating costs. Creating flexibility in machine design is also important to readily adapt to a variety of material and package options. But, delivering higher standards of operation while remaining cost effective is another key element.”
Despite poor economic reports though, Wilcox sees package machine sales to be very good for many companies at this time.
Costs are an issue
When it comes to costs, everyone is trying to control them, admits Derek Jones, senior marketing product manager at Lantech, Louisville, Ky. Jones says his firm experienced a downturn in sales back in 2008 like everyone else in the industry. Some bakers and snack producers are taking advantage of the current economy by upgrading and/or retrofitting existing equipment with the latest innovations.
“Many understand that the return on investment with recent innovations will have a short payback period,” says Jones. “But 2011 has been a banner year for sales. With that in mind, one of the best ways to keep tabs on costs is to make sure that shipping charges are correct. By weighing every load you ship for quality and freight costs, you are able to ensure that you’re being charged correctly.”
In addition, he says that understanding customer’s needs help his firm continue to be the leader in innovation in the industry. “Customers want peak performance,” Jones states. “They also want all-in-one weighing and stretch-wrapping machines that have a small footprint, are durable and keep operators safe. But it’s a challenge sometimes in educating our audience that all stretch wrappers are not [created] equal.”
Lantech’s EZ Weigh integrated scale with semi-automatic stretch wrapper, which was launched at September’s Pack Expo Las Vegas, meets those demands, he points out. “EZ Weigh weighs every load to optimize load quality and freight costs. The machine saves space and has a new, tilted skirt turntable design. The turntable resists impacts from fork trucks and pallet jacks. The weighing system is integrated under the turntable instead of with the entire machine. This helps improves weight accuracy as items only on the turntable are weighed.”
Improvements in containing loads is one of the greatest opportunities for growth in the package handling equipment market, Jones points out. “It’s critical to ensure that every load shipped meets ‘good load’ criteria. Good loads are bonded to a pallet to prevent shifting during transit. The stretch film used must be evenly applied to the load, without long or dragging film tails that could get caught on downstream equipment.”
Hygienic design counts
Dorner Manufacturing Corp., Hartland, Wis., agrees that the focus is not only equipment’s material construction but also hygienic design. “Customers are of the mindset that they will own this equipment for a long time,” says John Kuhnz, director of marketing. “Paying attention to equipment design and construction leads to a lower cost of ownership over the life of the equipment. This is a direct result of changes in overall cleaning practices in terms of increased frequency and to include areas in the facility that otherwise are not considered. In addition, the packaging lines in some applications are in closer proximity to the production areas, so customers opt for stainless steel and other corrosion-resistant materials. This is driving sales of sanitary designed and constructed equipment. It’s also impacting accessories often used with the equipment.”
Kuhnz says that customers indeed expect higher performance and some of it focuses on cleaning. “They want to minimize planned downtime and, if possible, eliminate unplanned downtime,” he points out. “Designing equipment with features that make cleaning easier and more effective reduces planned downtime for sanitation or allergen washes. Designs on our equipment like tip-up tails, belt lifters and clean-out windows address these requirements. Customers are able to access these components, to clean the inside of the conveyor frame in seconds without tools.”
He believes that sanitary equipment is evolving every day. “Each time a piece of equipment is manufactured, suppliers and customers work on ways to make the equipment more sanitary.”
Dorner continues to invest in “smart” conveyance. “Smart” features go beyond sanitation and into conveyors that are easier to implement, communicate and interface with emerging technologies and packaging, Kuhnz says. The company offers a diverse range of conveyors and unit-handling solutions to meet these trends. There are conveyors for dry areas as well as wipedown and washdown platforms, available in both aluminum and stainless steel. “Each conveyor platform has hygienic design features required for a targeted environment within the food production facility,” Kuhnz reports. “And each platform has a set of conveyor features or accessories that allows for tailoring to each customer’s application.”
Where Dorner’s washdown systems are concerned, the most popular feature is the tip-up tails, which allow for quick access to internal frames for sanitation. On its dry conveyor platforms, the SmartSlot creates a smooth side on the exterior but still allows for the fast attachment of automation components. “In other words, there are no T-slots that could catch product debris,” he says.
The AquaPruf sanitary conveyor line is also designed for fast, effective sanitation that allows production lines to start running again quickly. “This is a real dollar saver,” Kuhnz points out.
Another trend that Dorner sees is the increased use of flexible package and pouches. “They bring new challenges with respect to their handling,” Kuhns acknowledges. “Another trend is future needs planning with package handling systems. Can a system be designed for a larger package, a smaller package or accept a 50% increase in volume? These discussions are taking place on each system design as companies look for greater ROI from packaging equipment automation. But for our role in package handling systems, I’d like conveyors to lead the way in hygienic design and sanitation features,” says Kuhnz. “Sanitary equipment is evolving every day.”
Robots get a grip
Weldon Solutions, York, Pa., builds robotic palletizing systems that it considers are the most flexible way to load multiple pallets of different products at the same time. “This requires that the robot’s end-of-arm tool (EOAT) be flexible enough to securely handle a variety of items,” notes Charles Gales, manager of automation sales at Weldon. “Our UniGripper has a matrix of valves that create a vacuum across the surface, and is capable of picking up one or multiple cases,” he says. “The compliant face of the UniGripper only creates a vacuum where cases are present. That allows for handling of different case sizes with no changeover. This is particularly helpful for CPG companies that change case sizes frequently during the production day or over time. The UniGripper can also automatically adapt to new case sizes. Once a new product or product size is programmed into the robot, that new information is ready to be handled by the UniGripper.”
Lowering cost of ownership
Dynamic Conveyor Corp., Muskegon, Mich., launched a new line of conveyors to the food processing and food packaging industries at PackExpo Las Vegas 2011, says Jill Bartka, president. “In addition to being quick and easy to clean, which saves time and money, the new line offers a unique benefit of reconfiguring the conveyor layout when the needs of the processor change.”
The company’s DynaClean conveyors are eco-friendly and sustainable, she points out, and reducing the ecological footprint is becoming a priority for many food companies. “Lowering the total cost of ownership is typically even more important to processors as costs continue to rise and it becomes more and more difficult to make a profit,” she says. “The DynaClean line is a response to these needs by allowing the end user to quickly and easily clean the conveyor, saving time and labor and other resources. This also saves changing the conveyor configuration with new segments of a different length or angle, preventing the conveyors from sitting unused and forcing the processor to purchase a new conveyor.”
Bartka says that when her firm designs a new package handling systems today, one of the most critical factors is that time is money. “Customers need conveyors that are quick and easy to clean. We design systems to include optional belt lifters that allow for access within three seconds to the underside of the belt and the internal conveyor components. The ability to remove the belt, belt supports, the motor and the return within in a few minutes without tools gives easy and very quick access for a thorough cleaning and sanitation. The conveyor can be reassembled after cleaning almost as easily as taking it apart.”
While the snack food and bakery markets are relatively new to Dynamic Conveyor, Bartka says there are great opportunities. “Educating processors on these new options in conveying that weren’t available just a few months ago is exciting for us and the processors. We’re eager to educate them on the fact that they can reduce their costs of conveyor ownership with a quick and easy-to-clean system that’s reconfigurable.”
Partnering with Intralox, Harahan, La., Dynamic Conveyor will soon offer an option for Intralox’s ThermoDrive belts on DynaClean conveyors. “An innovative, patented technology, ThermoDrive is the first to combine the best features of modular plastic and traditional flat belts.”
Solving denesting difficulties
Customers are also looking for solutions to difficult denesting tasks brought on by the need to reduce shipping costs. Because tray and clamshell package manufacturers are asked to reduce the size and weight of their denesting features, trays now nest closer together, making them even more difficult to separate, states Paul Grieger, inside sales for Axis Automation, Hartland, Wis. “Tray and clamshell manufacturers need to be able to make trays with much smaller denesting features, or possibly even none at all,” Grieger says. “We’re seeing a sharp increase in demand for our AXIS denester, which doesn’t use conventional denesting methods.”
Launched in the spring, the AXIS denester was developed to answer the call of rising fuel surcharges, increasing labor costs and a demonstrated need to perform without suction cups. It denests difficult containers such as certain foam structures. Because of this, trays don’t need to have flat bottoms. “Trays can now have ridges across the entire surface below the product, which translates into less product breakage and better presentation,” he says. “Cookies or crackers can stay nested in the tray. And the denester’s design works well with trays that have much smaller denesting features or in some cases, none at all. Smaller denesting features means that trays nest closer together. That’s ultimately better for the environment. Less space between trays means fuel savings because there are fewer cases to ship for the same quantity of trays or clamshells.”
Grieger agrees that sanitation is always an issue. “A stainless-steel construction makes cleaning and sanitation much easier. And easier changeovers are also very important. High performance is always a requirement as well. A denester can be well built, easy to clean and a real bargain, but if the machine isn’t up to the task at hand, it’s going to be moved to a dark corner where it will sit and gather dust.”
Display-worthy and enviro-friendly
Display-ready packaging that significantly reduces labor costs when stocking shelves is also seeing big demand at Eagle Packaging Machinery, Miami. “Another trend we see is packaging that’s environmentally friendly-using less packaging to reduce the overall packaging footprint,” says John Brown, sales and marketing coordinator for Eagle. “Our POLOK tray former uses no glue or tape, which facilitates recycling. Customers also look for machines that can pack or form different tray sizes and are fast and easy to change over. The flexibility of the POLOK tray former allows us to accommodate various tray-size ranges unique to each customer.”
The former creates one- and two-tuck, multi-tuck and intricate trays, with or without a lid, in small and large-size formats. “Secondary packaging that doesn’t touch the product directly, productivity is paramount,” Brown adds.
In addition, the Boxxer Auto Lock case erector uses no tape or glue when erecting RSC/HSC-style cases with auto-locking bottoms. Built with a low maintenance mechanical drive, a heavy-duty welded steel frame and interlocked safety gates and doors, the Auto Lock provides quick-size changeovers in a compact footprint. Venturi vacuum technology is used to erect the trays, and all functions are controlled with a PLC color touchscreen. Also using vacuum technology is Eagle’s Z.ZAG palletizer, which automatically picks up one or two cases and places them on a pallet. The system can be used with several production lines.
“There’s another trend in the industry to lighten the container board without sacrificing the required strength and integrity needed, all of which will influence the future designs of equipment,” Brown points out. “Today, we see more need for equipment that’s simpler for operators to learn and use and for maintenance staff to service.”
Regardless of what’s being packaged and shipped, this and many other package handling systems are being designed to fill the bill on baker and snack manufacturer needs.
Looking for a reprint of this article?
From high-res PDFs to custom plaques, order your copy today!