Coronavirus
How flavor-supplier FONA is navigating COVID-19
Flavor company, which was declared essential, is training staff on sanitation procedures (including executives), offering digital events, and staggering shifts to increase social distancing.
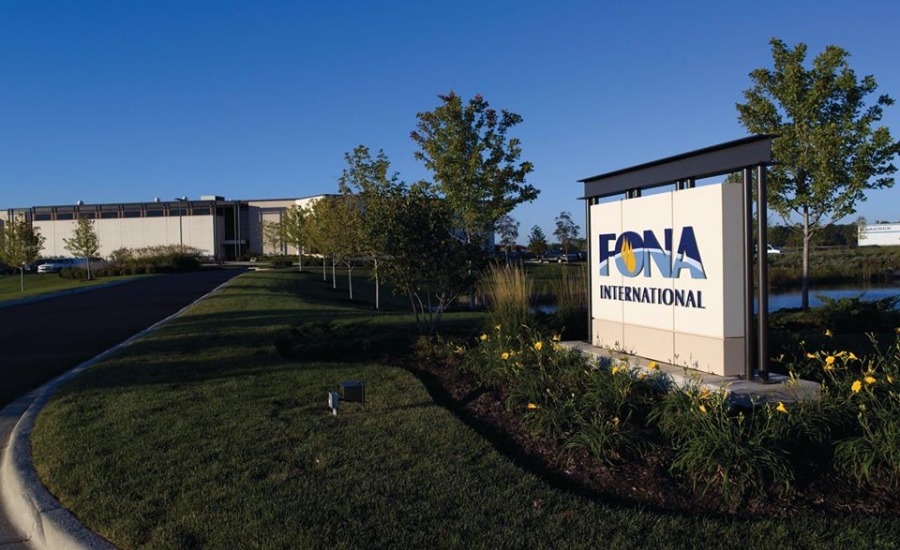
The current global COVID-19 pandemic is impacting the entire supply chain, including flavor suppliers.
FONA, which is based in Geneva, Illinois, creates and produces flavors for many of the largest food, beverage, and nutritional companies in the world. The company has seen a number of changes as a result of the pandemic. And Deirdre Burgess, director of corporate communications at FONA, recently took some time to discuss how the ingredient company is navigating those things.
Below, Burgess talks about how the company is training staff on sanitation procedures — including executives — while also managing supply chain issues and offering digital alternatives to in-person events.
Is FONA having any disruptions to its supply chain as a result of COVID-19, and if so, how is it handling it?
FONA put together a supply chain-focused task force in February to focus on the COVID situation, which at that time was predominantly getting attention in China.
That team continues to meet almost daily, to analyze information and mitigate any potential impact.
So far, thanks to that proactive approach and our amazing network of suppliers, FONA has been able to avoid any supply chain issues. That means we have been able to provide for our customers and help them keep grocery and pharmacy shelves stocked.
What can confectionery manufacturers expect as far the ingredient supply chain is concerned? Are things being delayed? Are there some products more impacted than others?
So far, delays in the industry seem to be around transportation and shipping more than supply issues but the situation is quite dynamic. Time will tell how this all evolves.
How can confectionery manufacturers best deal with any potential issues that might come up as a result of COVID-19?
At FONA, we believe the best approach is to be proactive and communicate openly with your partners and vendors — and even with your competitors. We believe that working together is the best way to keep moving forward through these unique times. At FONA, we advise to share your obstacles openly. You never know who might pipe up with a solution or who can connect you with someone who can help.
How is FONA handling its operations during the pandemic? Are certain facilities shut down? Are staff working at home? Etc.?
FONA has taken this very seriously since the early days of the COVID-19 spread. An action-focused pandemic preparedness team that began meeting in early March, with a focus on protecting employees and mitigating any potential risk. This team meets twice a day most days, to review recommendations from the CDC, OSHA and the WHO, and to talk through all the related issues from a safety and culture standpoint. We constantly do an inventory check on safety and hygiene equipment to make sure employees have everything they need to stay well. The team works to quickly act on any issues or needed communications.
Like our customers and vendors, Homeland Security has deemed FONA as essential to the infrastructure and the food and medical supply of the nation. It’s an honor and a great responsibility — and requires great care to do everything possible to keep employees safe and well.
One of the core values at FONA is “do the right thing,” and it is one that has come into play quite often in these recent months.
FONA instituted increased sanitation and hygiene practices, as well as employee education efforts in early March. Employee meetings featured in-depth education about the virus, hygiene and sanitation. Additional trainings were held and signage distributed and posted around the building in both English and Spanish.
Staff that are able to work from home started doing so a week before the Illinois shelter-in-place order. Shifts and “days” in and out of the facility have been staggered for many teams to increase social distance.
FONA has also been doing deep-clean, food-safe sanitation of the full facility regularly. In fact, volunteers from across the business — including several executives — were recently trained in special equipment to do deep-cleaning sanitization. That is in addition to third-party facility sanitation that is happening regularly, and the habits of employees to constantly sanitize their work spaces.
Has FONA canceled any events because of the coronavirus? Are they replacing them with digital options? How is the company handling that?
FONA canceled its Flavor University courses in March and April. That included a Flavor 101 course to be held at our facility in Geneva and regional classes in Dallas, Santa Ana, California and Toronto. While those will be rescheduled, the FONA team didn’t want customers to miss out on the important professional development. So we jumped on the opportunity to try out some fun new things.
What’s exciting is how quickly FONA got moving with webinars and other virtual offerings. We wanted our customers to be able to keep moving forward, even in small ways. The response to the virtual offerings has been outstanding, with 400-500 food and beverage professionals tuning in. Flavor University faculty even received overall scores of 10/10 from attendees. In fact, for the Flavor University webinars, FONA maxed out the number of registrations and had to sign up for a bigger webinar package to meet the demand. That feels like a good problem to have.
Anything else you would like to add?
Here at FONA we are talking about what comes after all of this. We know that after such inflection points, significant social change follows. Thinking about what that looks like for FONA’s customers, our employees, and our business is key to the future.
Looking for a reprint of this article?
From high-res PDFs to custom plaques, order your copy today!